#1 Design
- What happens in the design phase?
Describe your challenge, and we'll design your solution.
The design process starts with an idea or opportunity that we want to explore. This can be an unfulfilled customer need, a customer challenge, a new market, or a new technical solution not addressed by competitors or generally in the market.
What to expect
Our sales managers are often the first to talk to the customer about their challenges.
It is normally the sales manager who comes up with the basic concept in collaboration with the customer. They communicate directly with the technical resources at the customer. We will work with our client to find the right components and composition.
Our sales department have great experience and are notoriously interested in the technical part of our services. This provides a good transition from sales to design and production, because this assures a deep understanding of the customers need and high technical quality.
Based on many years of experience, we know most of the solutions and components on the market, and will therefore easily see what kind of solution will satisfy the customer's wishes.
How it works
The design process itself contains several more or less fixed steps.
From the idea phase we will have set goals and expectations. This is followed by extensive analysis to gather information and data. We will research market and/or customer requirements, market potential and size, explore the environmental impact, risk analysis and more.
In cooperation with technical supervisors and the workshop, we will draw the first solution concepts in the form of descriptions, sketches or models.
This is further discussed and prepared together with the customer, before we proceed with GA drawings.
GA-drawings illustrate dimensions and functionality. Size matters, and the final solution should preferably not take up any additional space.
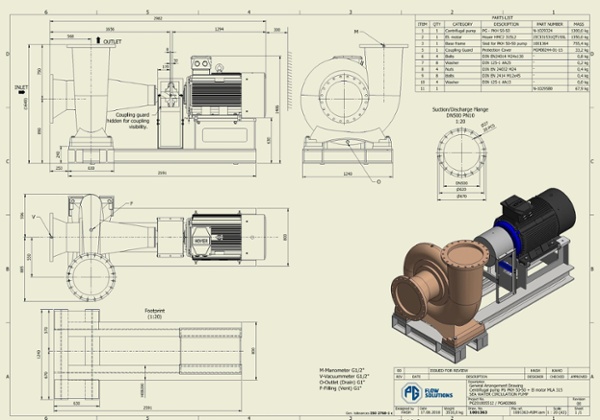
Throughout the design process, we have a close dialogue with the customer, several follow-up meetings and clarifications along the way.
We will involve a number of internal resources to ensure competence across disciplines. Normally you will meet a broad technical team with a technical manager in lead.
As we approach a finished design, we will move on with production drawings which shows all the components we are going to include, and how these are assembled together. In this phase, all parts must be clarified. Meaning mechanical parts, automation, systematics and electrical components.
Extensive analysis
We use CFD analysis, FEA analysis and advanced 3D models to understand the materials stability, examine the fluid flow and to get the complete details. Based on analysis we can adjust and optimize.
FEA analysis is a computerized method for predicting how a product reacts to pressure, vibration, heat, fluid flow, and other physical effects.
We use FEA analysis to examine whether materials used in the product are able to withstand forces the product will be subjected to during it's lifetime.
We are experienced in FEA reports complying with common DNV- and Norsok standard.
CFD Analysis is a numerical analysis and data structures to analyze and solve problems that involve fluid flows.
We are experienced in Ansys Fluent, the industry leading software for advanced flow simulations, enabling us to deliver fast and accurate results.
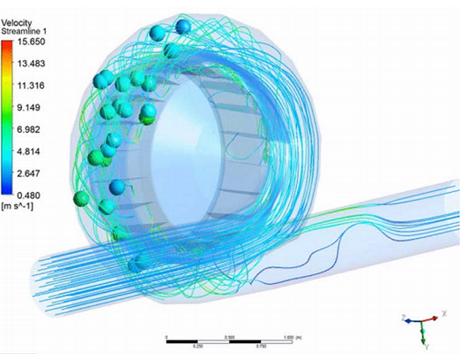
Examples of analysis we carry out
We can run analysis to check pump capacity. E.g. connecting a pipeline with it's components to a pump. Will the pipeline match the pump capacity?
Within aquaculture, there are strict rules for how to transport live fish. High pressure can damage the fish. At the same time there must be enough propulsion to carry out transport. We conduct analysis to find the optimal fluid flow for efficient and safe transport.
To develop sustainable solutions is important to us. Companies want to work energy efficient and not use more energy than they need.
By using flow analysis, we can estimate important flow characteristics and optimize energy use and pressure anomalies before testing. This can contribute to significant cost reductions on specific projects.
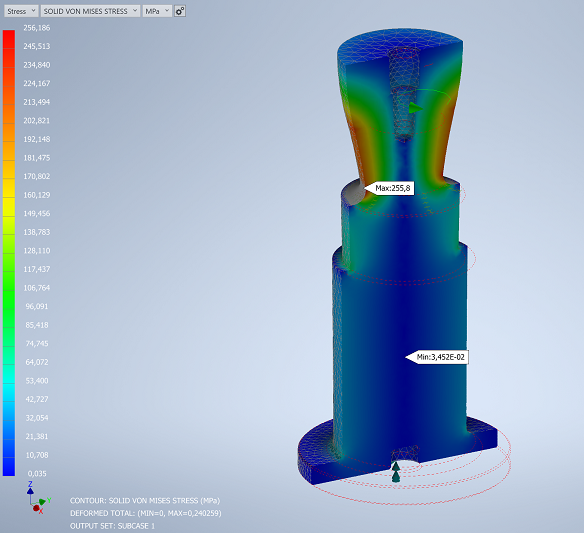
How to get started
View next steps. Learn how we build, test and commission our products and solutions.
#2 Build
Now, let's build it!
We cut, bend, machine, weld, assemble, treat and test a variety of component in-house. From design we have detailed steel drawings that describes which parts we must process.
When all the steel parts have been made and welded together, we will normally carry out surface treatment with paint or acid pickling.
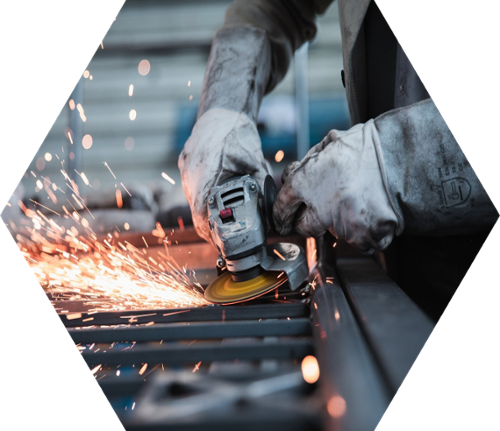
#3 Operation
We'll take care of you.
For some projects, our presence will be needed to carry out assembly and commissioning, other times the customer takes care of this process with support from us.
Our main goal is to verify that the systems and components are installed and operate according to project- and client requirements.
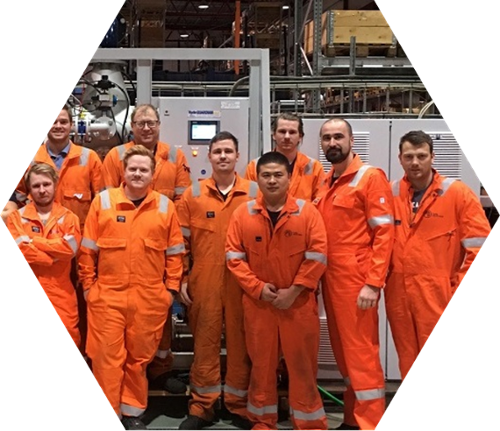